Your Benefits
Reduced Machining
Products that require machining can be optimized by near-net-shape parts made with our processes. Particularly cost-intensive and difficult-to-machine materials such as titanium or high-alloy-steels create highly profitable applications. Another application are large scale blanks that are not available on the current market for semi-fished and raw materials.
Optimized Supply Chains
Cast and forged parts, especially small batch sizes, can be substituted by components from PA-Labs with significantly shorter delivery times. Furthermore, by manufacturing different types of components on one WAAM system, complex supply chains can be simplified and manufacturing can be centralized in a robust and resource-saving way.
High Performance Components
PA-Labs enables innovative and unrivaled applications for which there are no alternative manufacturing processes. These include closed hollow structures for lightweight construction or multi-material applications, e.g. with locally dissolved wear or corrosion protection layers. Furthermore, we enable innovative concepts of mass customization.
Circular Economy
Metal components that are subject to heavy wear can be reconditioned promptly and do not have to be scrapped. These applications are especially interesting for low cost parts in large quantities that could not be reconditioned economically before.
What we offer
Additive manufacturing holds unimagined potential for a multitude of innovative applications – but also for false expectations and disappointments. The complex process events in the welding arc with temperatures beyond 13,000°C or diverse material compositions that pass through all aggregate states in the manufacturing process require profound expertise.
After years of engineering work, however, complex process and material behavior are no longer a book sealed with seven seals for us but the content of numerous, own scientific publications. Now, this knowledge and experience is available for your application.
Key features of Plasma Additive Machines
coming soon…
Development & Consulting
As an expert in your domain, you develop advanced products and components. The further you drive progress in your domain, the higher the demands on your components become. Often, new designs can no longer be manufactured using old processes.
Replacing one process with another does not always meet all the requirements arising from your task. In this case, basic work is required first. We see ourselves as your partner for additive manufacturing and do not leave you alone after the development of new manufacturing concepts.
Together with you, our specialists analyze the requirements that arise from your products or components. In doing so, we take into account internal company restrictions as well as upstream and downstream production steps.
The requirements for your components are complex. Equally complex is the selection of the best materials for your applications. In addition, synergy effects can be achieved by combining different materials, combining the best properties of the materials.
In this case it is good to have a reliable partner. A partner who can advise and test independently of a manufacturer’s product range. Until your welding task is solved.
The development of challenging products and components often involves demanding requirements. As a result, the field of additive manufacturing is also developing continuously. In particular, topics such as lightweight construction, multi-material construction, cooling concepts and the accompanying increased production have ensured constant progress in recent years.
We provide you with the chance to bring you and your employees up to date in the field of additive manufacturing and joining technology know-how by conducting individual training courses. Our training courses can cover a wide range of group sizes, from individual courses to entire teams, and take into account the different levels of knowledge of the participants. We customize each training course in the design phase according to YOUR requirements and wishes.
Our partnership with the ISF of RWTH Aachen University enables us to introduce, link, explain and demonstrate both theoretical and practical training content within the framework of a training course.
The benefit of each training course comes from the application and use of the newly acquired knowledge in the industrial working environment. We see ourselves as a partner in additive manufacturing who supports you and your employees with our many years of practical experience, working closely with you to implement and optimize manufacturing processes or to prepare investment decisions.
The cornerstone for exploiting the full potential of additive manufacturing lies in component design. We accompany you from the first sketch to the complete implementation of your component. Our design engineers use the latest 3D-CAD software and will be happy to support you.
We have a well-equipped laboratory with all the necessary tools for sample preparation to assess and verify the quality of your components. Accordingly, we can offer you the following services:
- Preparation of macrosections
- Preparation of microsections
- Creation of hardness profiles
- Creation of tensile tests
- Determination of notched impact strength
You need a large steel housing for your machine? You initially consider having it casted, but the lead times offered create new challenges for you? By substituting classic manufacturing processes such as casting, milling or forging with 3D printing of your metal components, you will always be one step ahead.
Whether you need single parts, prototypes or a small series: Increase your efficiency by entrusting us with the production of your parts. The on-time delivery of your products with high-quality components is just as important to us as the flexible production readiness.
Mechanical engineering
Our team’s vision is to radically reduce the barriers to entry of arc and wire-based 3D printing of metal components. This can make the technology accessible to the entire metalworking industry, in turn creating new applications for arc and wire-based manufacturing.
In addition to the possibility of purchasing your system, we also offer an attractive leasing package. This allows us to reduce barriers to entry and investment risks while familiarizing you with the new technology.
The system provision is supplemented by a service offer that supports you in the application and operation of your 3D printing system. Don’t hesitate to contact us about our individual service/maintenance programs.
Do you need a shielding gas or a filler metal that is particularly well suited to your application? Do you want to increase your productivity and reduce your non-productive cooling times?
We will be happy to provide you with customized consumables and advise you on all the details.
Customized Integration
There is still an old welding power source in the basement?
You were just about to scrap your industrial robot?
With our innovative control approach, we can combine already available system components (manufacturer-independent) into a functional additive manufacturing cell.
Interested? Contact us!
The integration of additive manufacturing into existing production lines is one of our core competencies. We are happy to support you in the coordination with upstream and downstream processes, as well as in the transfer and interpretation of data.
The parametric user interface of the control can be used intuitively by unskilled employees immediately – design skills and process knowledge are not required.
The Process
Additive manufacturing of metallic components involve a large variety of different processes that often leave more questions than usable options. Which of these processes is suitable for my task? Is it only a marginal phenomenon in the rapidly advancing field of additive manufacturing? What is the level of technological maturity for industrial use?
Arc welding, which is a good hundred years old, has produced a wide and affordable range of wire materials and is characterized by maximum productivity and flexibility. So why isn’t everyone already using this technology? The highly productive arc process requires targeted monitoring and control, which are at the core of our unique process technology.
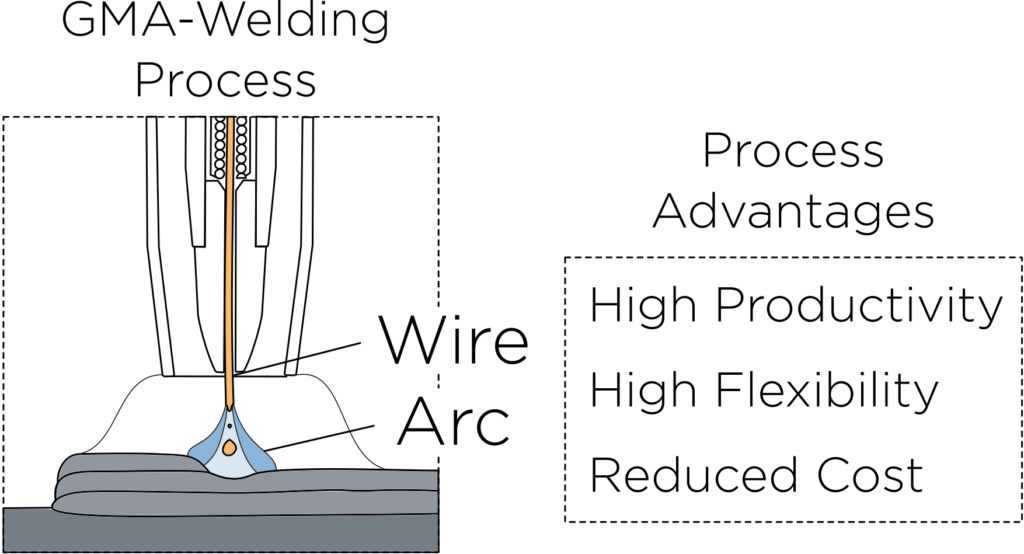
Our Technology
Groundbreaking Innovation, outstanding know-how and unlimited possibilities are inflationary used buzzwords, that make even current currencies blush. What are our convincing arguments? And most importantly, what is your gain for your specific application?
At Plasma Additive, years of engineering experience from welding technology meet novel and thoroughly digitalized automation approaches and process chains. According to our approach, quality monitoring and control are not an add-on, but an inherent element. Multi-material applications not a distant concept, but proven reality.
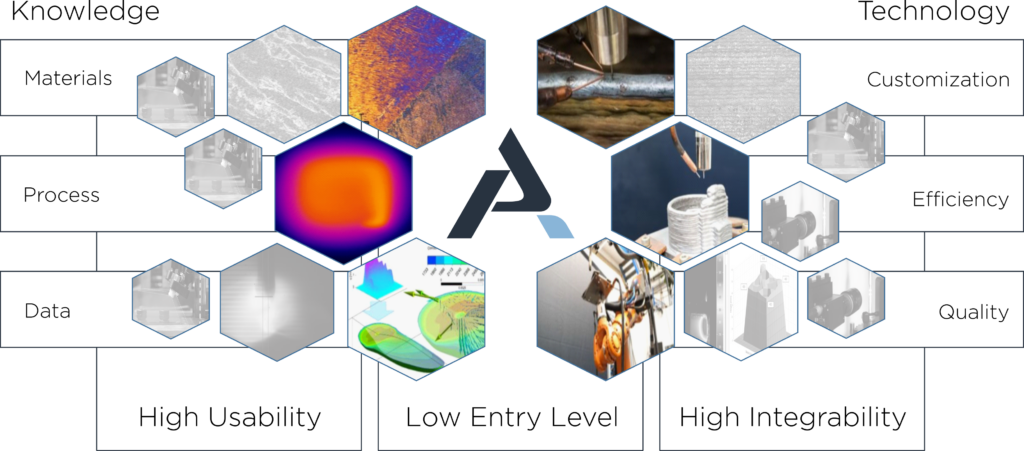
One of the best arguments for good technology is when it simply works without being to the fore. For this reason we put emphasis on high usability, which allows even untrained rookies to access WAAM. We have a PhD in this field, so you don’t have to. Furthermore, our digitilization approach allows seamless integration into your production systems – as far as it is desired. And last but not least, our systems approach enables a low entry threshold. We have mastered the use of industrial robots, which allow great degrees of freedom. For specific applications, however, we also use portal systems that allow an uncomplicated entry.
Contact
You are interested in special WAAM-solutions and want to get in touch?
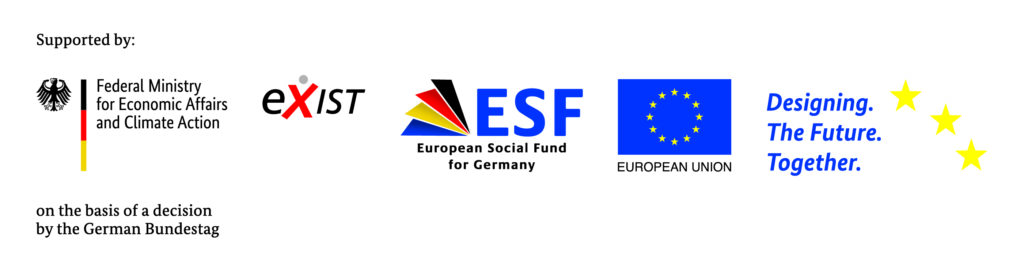
Das Vorhaben „EXIST-Forschungstransfer: APAM-Anlage“ wird im Rahmen des EXIST-Programms durch das Bundesministerium für Wirtschaft und Klimaschutz und den Europäischen Sozialfonds gefördert.